PWM Technology Overview
Although Pulse Width Modulation technology has been around for over 20 years, it has recently gained relevance with the increase in weed species that are resistant to plant protection products. Part of the resistance problem stems from not hitting the target with a full dose of active ingredient.
One of the advantages of PWM systems is the instant on/off of the solenoids, allowing the operator to spray right up to the edge of the field. Another advantage of PWM is that pressure is no longer tied to travel speed, as with conventional spray systems, so that pressure can be maintained across the field, and the spray quality (droplet spectrum) is the same at the start, middle and end of the spray job. As the sprayer slows down at the headlands of the field, the system delivers the same rate at the same pressure, with the same spray quality.
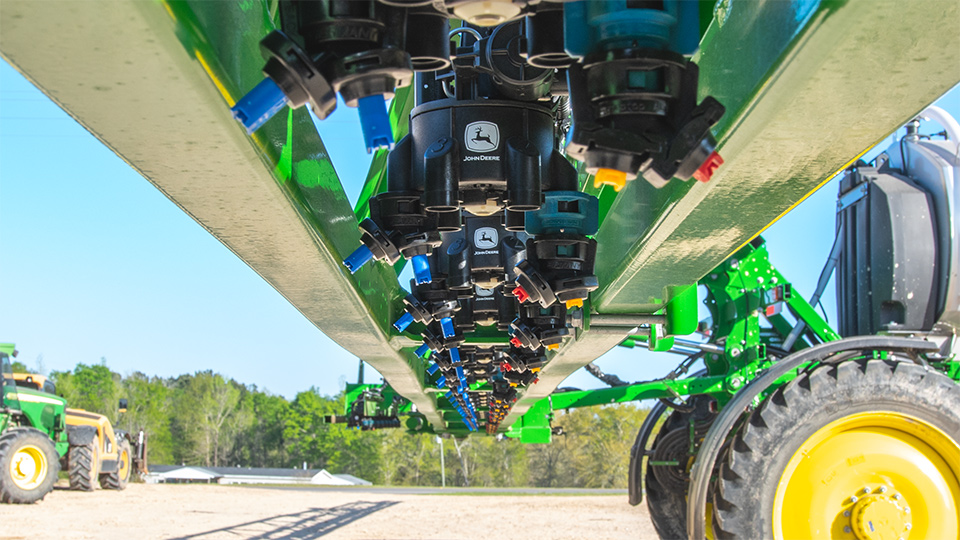
Not only do PWM systems have a greater speed range than conventional systems, but they also allow for more refined section control, or even individual nozzle control. This function prevents overlaps in spraying, and can lead to significant chemical savings by preventing over-dosing.
Finally, most PWM systems also include turn compensation as another feature. When the sprayer is turning, the end of the “outer” boom is moving much faster than the sprayer, which would normally result in under-dosing (again, promoting resistance), while the end of the “inner” boom is travelling more slowly and putting out a much higher rate. PWM systems compensate for these speed differences, controlling the solenoids to maintain the correct rate, by keeping the width of the pulse wide enough to deliver the proper flow. For small or irregular fields, turn compensation can provide chemical savings as well as a higher level of accuracy.
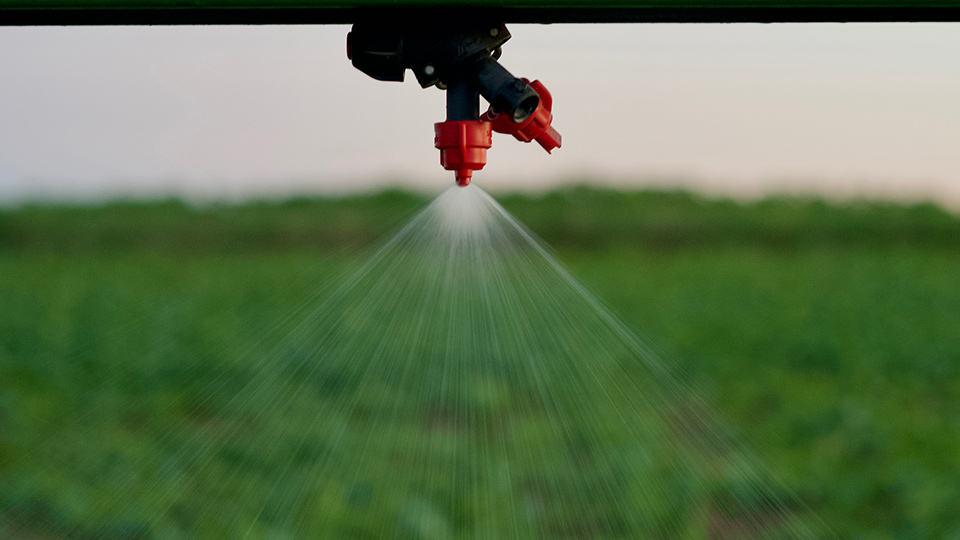
As with conventional spraying, choosing the right nozzle is critical with PWM spraying. Air induction nozzles are generally not recommended, because the multiple pulses per second do not allow the air inducing function to work properly. For this reason, Greenleaf Technologies offers different nozzles for PWM spraying, so that the operator can choose the optimal spray quality as well as the best spray pattern for the job.
The Softdrop nozzle is designed to deliver Extremely Coarse to Ultra Coarse droplets for systemic products like glyphosate, dicamba and 2,4-D, where drift control is of the utmost concern. The Blended Pulse™ and Blended Pulse™ DualFan are designed for coverage critical contact chemicals, providing a Medium to Coarse to Very Coarse spray quality. The SprayMax and SprayMax DualFan deliver the smallest droplets, Fine to Medium, and should only be used for insecticides, fungicides and other contact products when conditions allow for this type of spray quality.
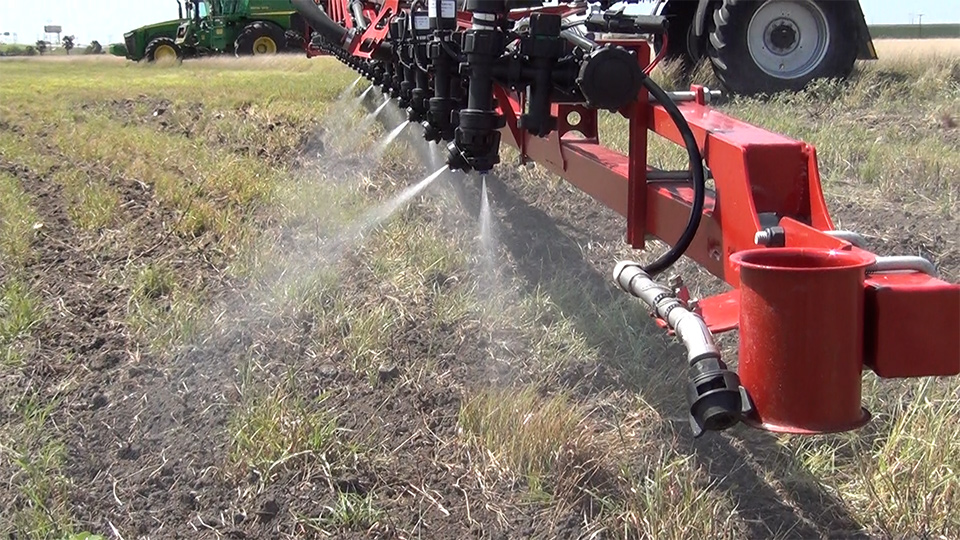
Selecting the right nozzle for PWM: Nozzle Size, Pressure, Frequency, and Duty Cycle
All SprayMax, SprayMax DualFan, SoftDrop, Blended Pulse™, and Blended Pulse™ DualFan Greenleaf Technologies PWM nozzles have been designated for use with PWM systems such as Aim Command™, Capstan Synchro™, Raven Hawkeye™, or John Deere ExactApply™ and other PWM spraying systems.
To size the nozzles, take the desired GPA rate and divide by 0.7, in order to target a 70% duty cycle. For example, if the application rate is 10 GPA, divide this by 0.70 to get 14.3. That will be the GPA to look for on the tabulation chart. This method will get good results for most use cases, for more detailed information on nozzle selection see our PWM Nozzle Selection Guide. If you need assistance with choosing the right nozzle for your application, please contact us directly.
The writings of Tom Wolf, Jason Deveau, and Sprayers 101 were used as reference material when developing the information provided above.